St Hugh’s Engineering students involved in key development projects
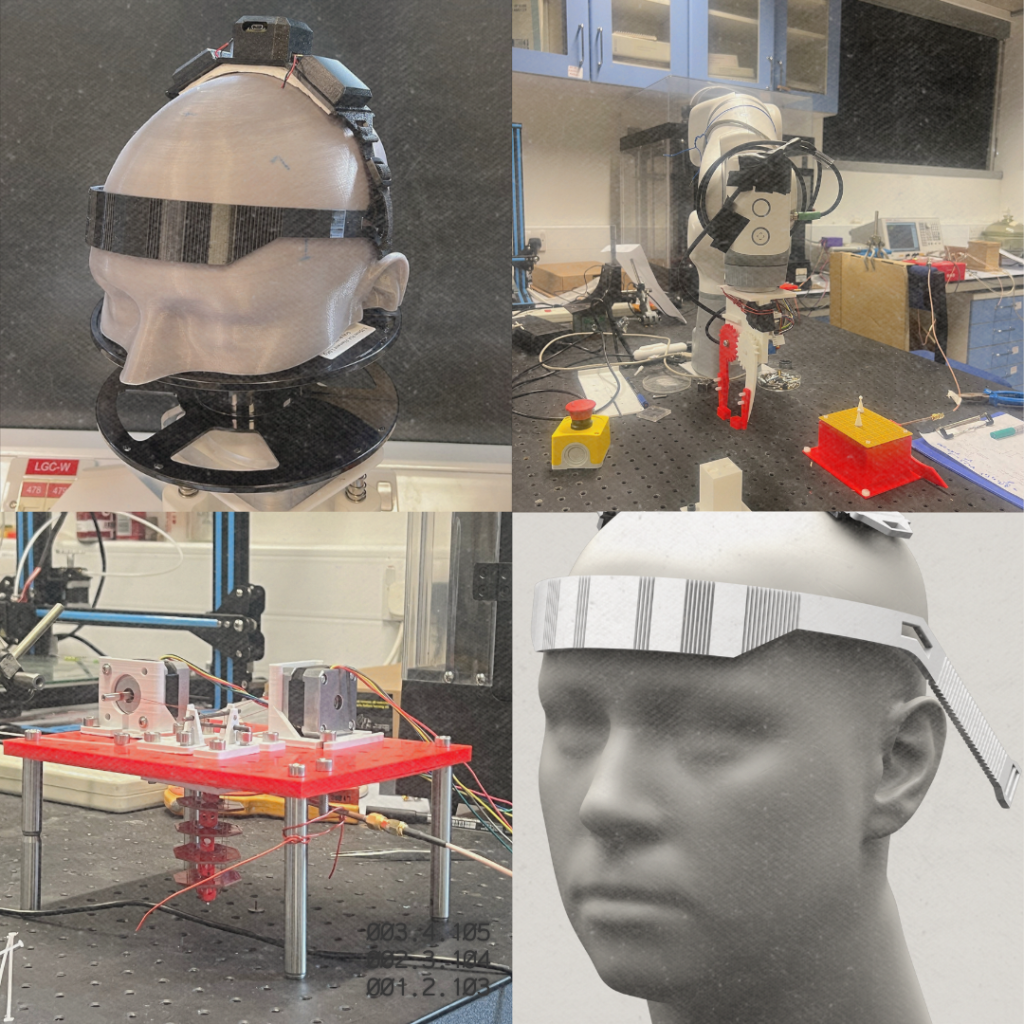
Congratulations to St Hugh’s third year Engineering students, Daniel Costache and Huirui Dai whose experiments during their summer internships have significantly contributed to the design of new engineering concepts for the future.
Daniel worked with Professor Tim Denison who holds a joint appointment in Engineering Science and Clinical Neurosciences at Oxford, where he explores the fundamentals of physiologic closed-loop systems. Daniel’s work has been crucial in developing a headband which will be used for Targeted Memory Reactivation (TMR) in relation to post traumatic stress disorder (PTSD) and depression. The headband Daniel was involved in developing has been part of a collaboration with the Neuroscience and Psychology of Sleep Lab at Cardiff University. He has been working consistently on developing and improving the headband with feedback from a patient advisory group as part of the collaboration. Daniel has designed the headband to be flexible allowing different electrode placement to cater for studies investigating different sleep stages and areas of the brain.
Going forward, the headband will be part of a project looking to use TMR, which is when a sound previously paired with learnt material from wake is played again during sleep to reactivate the memory. This headband will be used in projects looking at how we can manipulate emotional memories and how this applies to PTSD and depression. Designing the headband using patient feedback has been crucial to the project to allow for overnight data collection in the comfort of participants’ homes and increase where and when the data can be collected.
Daniel said, ‘The headband measures brain activity and uses a classifier to determine sleep stage, after which it applies a therapy (TMR) using the bone conduction speaker (middle rectangular part). I designed the mechanical part of the headband for FDM manufacture; every part of which was 3D printed, apart from the straps. In 2025, I will be working on turning the headband into a research platform for EEG (electroencephalogram) data gathering and varied therapy applications.’
For nearly 25 years scientists have worked on meta-materials which are engineered composites that can be designed to exhibit all sorts of interesting properties including the ability to make perfect lenses, create invisibility cloaks and send power wirelessly. Tutorial Fellow in Engineering, Professor Chris Stevens said, ‘In this work we are looking at using some types of metamaterials to perform sensing functions and replace the complex electronics in touch screens and robot sensors. Doing this makes the power consumption lower, the complexity lower and the overall cost lower whilst offering some unique new functions. The summer project was aimed at demonstrating some of the capabilities in test objects which included a simple robot digit and a flat localiser plate – something like a primitive touchscreen.’
During his internship in Professor Chris Steven’s laboratory, Huirui developed a robot proprioception experiment which has formed the proof of concept demonstration that is now the basis for a £2.7M ARIA grant application. Huirui said, ‘For the metal defect detection research, I programmed a robotic arm and designed a custom gripper mechanism, which I then implemented on the arm. This setup allowed the robot to automatically place chess-shaped targets at various locations on a metamaterial array surface, recording data to train our model. Using this data, the machine learning model could accurately predict defect locations. In tests, I manually introduced defects, fed the data into the model, and found that the predicted locations matched the actual defect positions precisely.’
For the robot proprioception experiment, Huiri worked with Engineering team to create an octopus-inspired robotic arm using a printed circuit board (PCB) structure with 3D-printed washers to separate layers. Fish wires connected different segments of the arm, allowing it to bend at various points when the wires were pulled. Resonant circuits were soldered onto the PCB, and by placing an optical probe under the circuits, they measured reflected signals. The team discovered that the bending of the arm correlated with shifts in the signal plot peaks, allowing them to predict bending angles based on the data. This effectively simulates proprioception in the robotic arm.